La méthode Six Sigma est l’une des approches les plus efficaces et structurées utilisées par les entreprises pour améliorer leurs processus, réduire les défauts et augmenter la satisfaction client. En 2024, alors que les entreprises continuent de se réinventer dans un environnement de plus en plus concurrentiel, l’application de la méthode Six Sigma reste un levier stratégique pour atteindre des objectifs d’amélioration et de performance.
Dans cet article, nous explorerons la définition et les origines de Six Sigma, ses principes clés, ainsi que ses avantages et limites. Nous aborderons également la manière dont cela peut être mis en place selon le type d’entreprise et de secteur d’activité, en vous fournissant des exemples concrets d’application pour maximiser votre efficacité et atteindre vos objectifs de qualité.
Qu’est-ce que la méthode Six Sigma ? – Origine et définition
La méthode Six Sigma a été développée par Motorola en 1986 sous l’impulsion de son ingénieur, Bill Smith. Elle visait à réduire les imperfections de production et à améliorer la qualité des produits en optimisant les processus de fabrication. Le terme « Six Sigma » fait référence à un niveau de performance où les défauts sont réduits à moins de 3,4 pour un million d’opérations, soit une amélioration significative en termes de qualité.
En 2001, Six Sigma a été popularisé et appliqué dans d’autres industries par des entreprises comme General Electric (GE) sous la direction de Jack Welch. À l’origine un outil spécifique pour l’industrie manufacturière, cette approche s’est rapidement élargie à de nombreux autres secteurs tels que la finance, la santé, l’IT et le service à la clientèle, en raison de son efficacité à optimiser les processus et réduire les coûts.
La méthode Six Sigma repose sur une analyse statistique des données pour identifier, mesurer, analyser, améliorer et contrôler les processus. Elle utilise des outils et techniques spécifiques, notamment le cadre DMAIC , qui est un acronyme représentant les cinq étapes clés du processus d’amélioration continue :
1. Définir : Cette première étape consiste à identifier clairement le problème ou l’opportunité d’amélioration, en définissant les objectifs du projet, les attentes des clients et les critères de performance.
2. Mesurer : Lors de cette étape, les données relatives aux processus existants sont collectées pour établir un état des lieux et mesurer les performances actuelles. Cela permet d’identifier les écarts entre la situation actuelle et les objectifs à atteindre.
3. Analyser : Une fois les données recueillies, il s’agit d’identifier les causes profondes des problèmes ou des variations. L’analyse des données permet de mieux comprendre d’où viennent les défauts ou les inefficacités dans le processus.
4. Améliorer : Cette phase consiste à mettre en œuvre des solutions pour éliminer les causes des problèmes identifiés, en optimisant les processus. Les améliorations peuvent inclure des changements dans les méthodologies de travail, l’introduction de nouvelles technologies ou des ajustements dans la gestion des ressources.
5. Contrôler : Enfin, il est crucial de mettre en place un système de surveillance continue pour s’assurer que les améliorations restent en place à long terme. Cela comprend la mise en place de procédures de contrôle et le suivi des performances afin d’éviter que les problèmes ne réapparaissent.
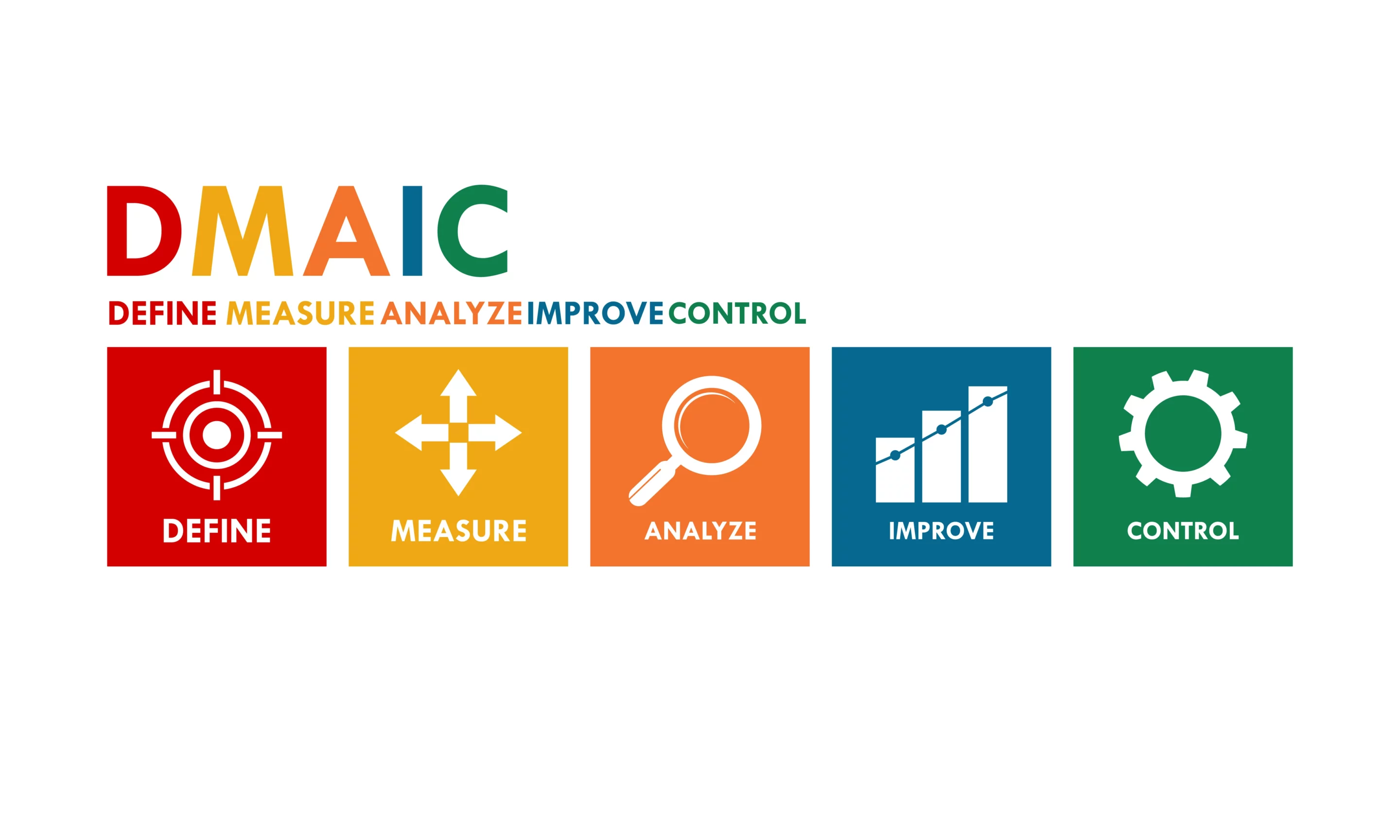
Le cadre peut également être appliqué dans le management de transition pour optimiser rapidement les processus au sein d’une organisation en mutation.
Le management, c’est l’art de faire les choses à travers les autres. – Mary Parker Follett
Les principes de la méthode Six Sigma
L’approche Six Sigma repose sur plusieurs principes fondamentaux :
Réduction des variations : L’un des objectifs clés de Six Sigma est de réduire la variation dans les processus pour que les produits et services soient conformes aux spécifications, ce qui mène à une réduction des anomalies et des coûts.
Amélioration continue : Six Sigma est un modèle d’amélioration continue. Il ne s’agit pas de se concentrer sur une seule phase de réduction des défauts, mais de créer une culture où chaque projet vise à améliorer progressivement la performance à chaque étape.
Orientation client : L’approche Six Sigma met l’accent sur l’amélioration de la qualité afin de satisfaire les besoins des clients. Cela implique la compréhension des attentes des clients et l’adaptation des processus pour mieux répondre à ces besoins.
Prise de décision basée sur les données : Contrairement à d’autres approches, Six Sigma se fonde sur des données précises et une analyse statistique pour orienter les décisions et prendre en compte les causes fondamentales des problèmes. Le lean management soutient cette démarche en fournissant des outils tels que la cartographie des processus et les analyses des flux pour renforcer la prise de décision.
En appliquant Six Sigma à chaque projet, les entreprises peuvent non seulement améliorer la qualité de leurs produits, mais aussi optimiser l’efficacité de leurs processus, créant ainsi un environnement propice à l’innovation et à la satisfaction des clients.
Les avantages de la méthode Six Sigma
L’implémentation de la méthode Six Sigma peut apporter plusieurs avantages considérables aux entreprises :
Amélioration de la qualité : L’objectif principal de la méthode Six Sigma est de réduire les défauts à un niveau acceptable. Cela permet d’améliorer la qualité des produits et des services, ce qui augmente la satisfaction des clients.
Réduction des coûts : En identifiant et en supprimant les défauts et les inefficacités, la méthode Six Sigma permet une réduction substantielle des coûts de production et une meilleure allocation des ressources.
Amélioration de la performance : Grâce à une gestion plus efficace des processus, les entreprises peuvent améliorer leurs performances, ce qui se traduit par une meilleure productivité et des résultats plus rapides.
Culture d’amélioration continue : En intégrant la méthodolgie Six Sigma, les entreprises créent une culture orientée vers l’amélioration continue, où chaque membre de l’équipe est impliqué dans le processus d’optimisation.
Avantages mesurables : Les projets Six Sigma reposent sur des données mesurables, ce qui permet aux entreprises de suivre les résultats et de vérifier l’efficacité des solutions mises en place.
En appliquant la méthodologie Six Sigma avec une approche de management efficace et l’engagement de toute l’équipe, les entreprises peuvent non seulement améliorer la qualité de leurs produits, mais aussi optimiser leurs processus pour obtenir des résultats concrets en termes de performance et de réduction des coûts.
Un leader est celui qui connaît le chemin, marche sur le chemin et montre le chemin. – John C. Maxwell
Les limites de la méthode Six Sigma
Bien que l’approche Six Sigma offre de nombreux avantages, elle comporte également certaines limites :
Nécessité d’une expertise spécifique : L’implémentation de Six Sigma nécessite des compétences spécialisées, notamment dans l’utilisation des outils statistiques. Les équipes doivent être formées à cette méthodologie avant de pouvoir l’appliquer efficacement.
Coût de la certification : La certification Six Sigma (Green Belt, Black Belt) peut représenter un investissement considérable pour les entreprises, notamment pour former les employés à cette approche.
Difficultés à grande échelle : Dans les grandes entreprises, la mise en œuvre de la méthode Six Sigma peut être complexe. La coordination de plusieurs projets à grande échelle peut entraîner des défis logistiques et organisationnels.
Temps et ressources nécessaires : Bien que Six Sigma permettra des améliorations à long terme, sa mise en œuvre demande un investissement en temps et en ressources, ce qui peut être un obstacle pour certaines entreprises qui recherchent des solutions rapides.
Bien que la démarche Six Sigma soit efficace pour résoudre des problèmes complexes, chaque étape de son implémentation nécessite une planification minutieuse et un engagement sur le long terme pour surmonter les défis liés à son adoption.
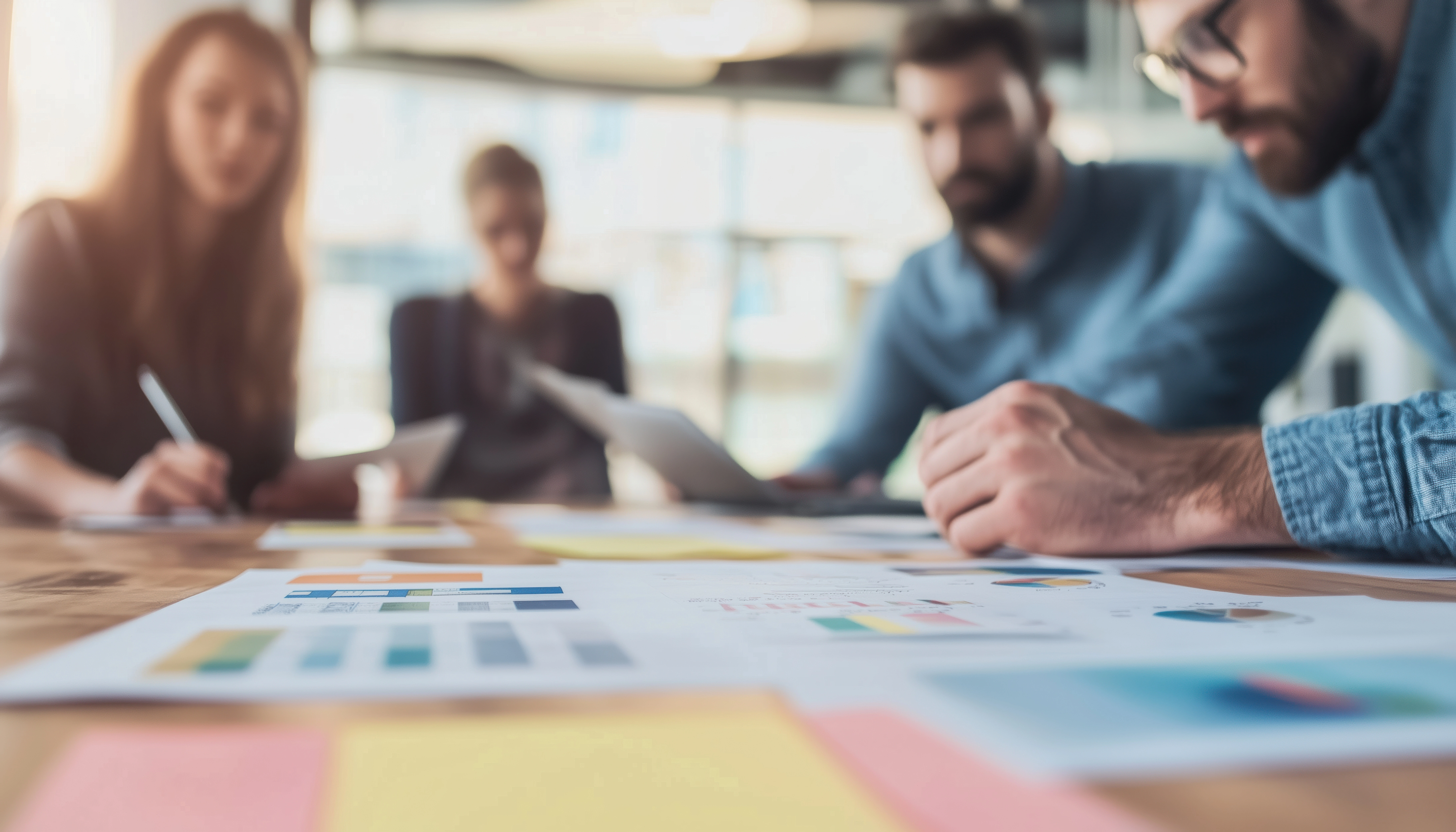
Comment mettre en place la méthode Six Sigma dans votre entreprise ?
L’implémentation Six Sigma nécessite de suivre un ensemble de phases structurées. Voici un aperçu des principales étapes de la démarche :
Définir le problème : Commencez par identifier un problème clé à résoudre, que ce soit une défaillance dans un processus ou une insatisfaction client. Utilisez les outils d’analyse pour établir les objectifs du projet.
Mesurer la situation actuelle : Recueillez des données et analysez les processus existants afin de comprendre où se situent les inefficacités. Les statistiques et les outils de mesure sont cruciaux à ce stade.
Analyser les causes : Grâce à la méthode DMAIC, analysez les causes fondamentales des problèmes en profondeur et identifiez les facteurs influençant la performance des processus. L’approche lean management peut également aider à repérer les sources de gaspillage dans les opérations.
Améliorer les processus : Utilisez les solutions proposées pour optimiser les processus, supprimer les défauts et améliorer la qualité et la performance.
Contrôler et maintenir les améliorations : Une fois les améliorations mises en œuvre, il est essentiel de contrôler régulièrement les processus pour assurer leur maintien et éviter les régressions.
Les méthodologies sont des outils puissants, mais c’est l’engagement de l’équipe qui transforme une stratégie en succès. – Peter Drucker
Exemple concret d’utilisation de la méthode Six Sigma
Etude de cas: Réduction des défauts dans la production de pièces automobiles
Contexte : Une entreprise de fabrication de pièces automobiles constate un taux élevé de défauts dans ses composants, entraînant des retours clients et des coûts supplémentaires. L’objectif est de réduire ce taux de défauts afin d’améliorer la qualité des produits et de diminuer les coûts de production.
Étape 1 : Définir (Define)
- Problème : L’entreprise a un taux d’anomalies élevé dans la production de pièces automobiles.
- Objectif : Réduire ce taux de défauts de 5 % à moins de 1 % en six mois.
- Équipe : Une équipe dédiée est formée pour traiter ce problème. Elle comprend un chef de projet Six Sigma (certifié Black Belt), des ingénieurs qualité, des opérateurs et des responsables de production.
- Projet : L’objectif du projet est d’analyser et d’améliorer le processus de fabrication des pièces automobiles pour réduire le taux de défauts.
Action concrète : L’équipe établit un plan précis en définissant les objectifs de réduction des défaillances, les rôles de chaque membre et les échéances du projet.
Étape 2 : Mesurer (Measure)
- Collecte des données : L’équipe mesure le taux de défauts sur plusieurs mois. Les types d’anomalies les plus fréquents sont identifiés, tels que des imperfections sur la surface des pièces et des dimensions incorrectes.
- Analyse des processus : L’équipe étudie les différentes étapes de fabrication des pièces pour comprendre où et pourquoi les anomalies surviennent, et quelle est leur fréquence.
Action concrète : Des mesures sont prises sur l’ensemble de la production pour établir un état des lieux. L’équipe identifie que les défauts se produisent principalement à certaines étapes de la chaîne de production.
Étape 3 : Analyser (Analyze)
- Identification des causes : L’équipe utilise des outils tels que le diagramme de causes et effets (Fishbone diagramme) et les 5 Pourquoi pour identifier les causes fondamentales des défauts.
- Il s’avère que la cause principale est une machine vieillissante qui affecte la précision des pièces.
- Analyse des données : L’équipe analyse également les écarts de dimensions des pièces et identifie que des variations de température dans l’atelier contribuent à ces erreurs de fabrication.
Action concrète : L’équipe découvre que la machine responsable des défauts n’est plus capable de maintenir la précision des pièces et que des fluctuations de température dans l’atelier de fabrication exacerbent ce problème.
Étape 4 : Améliorer (Improve)
- Propositions d’améliorations : L’équipe décide de prendre plusieurs mesures pour résoudre le problème :
- Calibrer régulièrement la machine pour maintenir sa précision.
- Remplacer certains composants usés de la machine.
- Réguler la température dans l’atelier pour éviter les variations qui affectent la fabrication des pièces.
- Test des solutions : Après avoir implémenté ces changements, des essais sont effectués sur la ligne de production pour évaluer l’impact sur la qualité des pièces.
- Résultats : Les anomalies diminuent de manière significative et le taux de défauts passe sous le seuil des 1 % visé.
Action concrète : La mise en place des améliorations est suivie d’un contrôle de la fabrication pour vérifier leur efficacité. L’équipe constate une réduction substantielle du taux de défauts.
Étape 5 : Contrôler (Control)
- Standardisation : Des procédures de maintenance préventive pour les machines sont mises en place, ainsi qu’un suivi rigoureux des températures de l’atelier pour éviter les écarts.
- Surveillance continue : Un tableau de bord est créé pour surveiller les taux de défauts et la performance des machines. Une équipe est responsable du suivi de ces indicateurs régulièrement.
- Formation : Les opérateurs sont formés aux nouvelles procédures et à l’importance du respect des standards pour maintenir la qualité.
Action concrète : L’entreprise établit un système de contrôle permanent, incluant des formations régulières pour les employés afin de garantir la continuité des améliorations.
Résultat final :
Grâce à l’application rigoureuse de la méthodologie Six Sigma, l’entreprise parvient à réduire ses défauts de fabrication de manière significative, tout en améliorant la satisfaction des clients et en diminuant les coûts liés aux retours produits et à la non-qualité.
Cet exemple démontre comment Six Sigma, à travers l’application du cadre DMAIC (Définir, Mesurer, Analyser, Améliorer, Contrôler), peut être utilisé pour identifier, analyser et résoudre des problèmes de qualité dans un environnement de production complexe.
Exemples concrets d’autres entreprises ayant appliqué Six Sigma
- General Electric (GE) : GE a utilisé Six Sigma pour améliorer ses processus industriels, réduisant les défauts et améliorant la productivité. Grâce à l’implication de managers certifiés Black Belt, GE a réussi à réaliser des économies significatives et à améliorer la qualité de ses produits.
- Motorola : Motorola, l’inventeur de Six Sigma, a utilisé cette méthode pour réduire les anomalies dans la fabrication de téléphones portables, augmentant ainsi la satisfaction client et réduisant les coûts de production.
- Amazon : Amazon utilise Six Sigma pour optimiser sa logistique, améliorer la gestion des stocks et réduire les coûts dans ses entrepôts. Cette application de Six Sigma a permis à Amazon de maintenir sa position de leader dans le secteur du e-commerce.
La méthode Six Sigma continue d’être une approche incontournable pour les entreprises cherchant à améliorer la qualité, réduire les coûts et optimiser les processus. Si bien qu’elle demande des ressources et une expertise pour sa mise en œuvre, les avantages qu’elle apporte en termes de performance et de satisfaction client sont considérables.
Adopter Six Sigma dans votre entreprise peut transformer vos processus de production, d’analyse et de gestion de la qualité, tout en optimisant les coûts. Pour les entreprises de toutes tailles, la méthode Six Sigma offre un cadre solide pour atteindre des résultats tangibles et durables.